Equipment
The equipment of the R&D centre varies, since it is kept up-to-date through constant retrofits, replacements and our own new developments. The Coatema R&D centre boasts unrivalled flexibility and a unique range of applications. It now also offers digital testing.
Here you can see an overview of the current laboratory, pilot and production plants used at the Coatema R&D centre at present:
Coating system Doctor blade Slot die system Commabar Working width DIN A4 (297 x 210 mm) Operating speed 0 – 4 m/min. Power supply 230 V, 50 Hz Design IP54 Dimensions (LxWxH) 1,100 mm x 580 mm x 530 mm. A good example is the design and manufacturing of a slot die for fluid coating operations. The basis of this pre-metered system is that there are two die body halves that are held together to form a slot for fluid to be deposited on a substrate.
Test Solution Coater
Coating system
Doctor blade
Slot die system
Commabar
Working width
DIN A4 (297 x 210 mm)
Operating speed
0 – 4 m/min.
Power supply
230 V, 50 Hz
Design
IP54
Dimensions (LxWxH)
1,100 mm x 580 mm x 530 mm
PDF download presentation
Coatema – The Test Solution
Test Solution R2R
Coating systems
Doctor blade
Slot die system
Commabar
Working width
100 mm
Roller width
150 mm
Operating speed
0.1 – 5 m/min.
Working direction
unidirectional
Winding diameter
max. 150 mm
Power supply
400 V, 50 Hz AC, CWW-32 A, 5P, 6h
Design
IP54
Compressed air
min. 6 bar
Dimensions (LxWxH)
2,200 mm x 1,000 mm x 2,000 mm

PDF download product brochure
Coatema Test Solution
PDF downloadpresentation
Coatema – The Test Solution
Easycoater
Coating systems
Doctor blade
Slot die system
Screen printing
Working width
max. 360 mm x 360 mm
Operating speed
ca. 0.4 – 4 m/min.
Dryer temperature
max. 120°C
Design
IP54 / EEx
Dimensions (LxWxH)
1,920 mm x 1,220 mm x 1,920 mm
Smartcoater
Coating systems
Knife system
Slot die system
Rotary screen system
Engraved roller system
Micro roller system
Dipping system (Foulard)
Working width
300 mm
Roller width
350 mm
Operating speed
0.1 – 10.0 m/min.
Tensile strength
10 – 250 N
Dryer
Hot air
Dryer temperature
max. 235°C
Exhaust Air / Consumption of nitrogen atmosphere
325 m3/h
Design
Atex / IP54
Dimensions (LxWxH)
5,500 mm x 1,050 mm x 1,855 mm
Basecoater
Coating systems
Slot die system
Double-sided-slot die system
Dipping system (Foulard)
2-roller system
Working width
300 mm
Roller width
350 mm
Operating speed
0.1 – 5 m/min.
Tensile strength
25 – 250 N
Dryer
Hot air
Dryer temperature
max. 235°C
Dimensions (LxWxH)
5,100 mm x 1,350 mm x 3,000 mm
Click&CoatTM
Coating systems
Slot die system
Knife system
Kisscoater
Engraved roller system
3-roller system
Screen printing
Powder scattering system
Working width
500 mm
Roller width
600 mm
Operating speed
0.1 – 2 m/min.
Tensile strength
10 – 250 N
Dryer
Hot air (UV, IR on demand)
Dryer temperature
RT – 235 °C
Exhausting air
ca. 1,500 m3/h
Design
Atex / IP54
Dimensions (LxWxH)
depends on combination
Linecoater
Coating system
Reverse Commabar
Working width
700 mm
Roller width
800 mm
Operating speed
3 – 30 m/min
Tensile strength
100 – 1.000 N
Dryer temperature
max. 180°C
Air circulation
5.000 m3/h per section
Exhaust air
5.000 m3/h per section
Dimensions (LxWxH)
19,000 mm x 2,500 mm x 2,600 mm
Red rock casino richmond bc canada. Visit the River Rock Casino Resort in Richmond BC for an unrivaled, ultimate entertainment experience. At this time, River Rock Casino Resort does not yet have approval to reopen Casinos in the Province of BC and therefore the date that we will be reopening our resort is yet to be determined.
Universal Coater
Coating systems
2 x 3 Roller system (for under and upper side)
1 x Slot die system
1 x Knife system
Working width
500 mm
Roller width
600 mm
Operating speed
1.0 – 30 m/min.
Tensile strength
75 – 3,500 N
Dryer
1) Floating dryer inert, Exhaust: 2,500 m³/h, Circulating air: 2500 m³/h
2) Conventional hot air dryer, Exhaust: 2,500 m³/h
Dryer temperature
1) Floating dryer inert: 140 °C
2) Conventional hot air dryer: 235 °C
Air circulation
2 x 6.000 m3/h
Exhaust air / Consumption of nitrogen atmosphere
270 m3/h
Design
Partially Atex / IP54
Dimensions (LxWxH)
19,000 mm x 3,500 mm x 2,700 mm
Deskcoater
Coating systems
Intermittend coating
Working width
500 mm
Roller width
600 mm
Operating speed
0.2 – 2 m/min.
Tensile strength
25 – 250 N
Dryer
Hot air
Dryer temperature
235 °C
Exhaust
ca. 2.500 m3/h
Design
IP54 / EEx
Dimensions (LxWxH)
4,250 mm x 1,600 mm x 3,100 mm
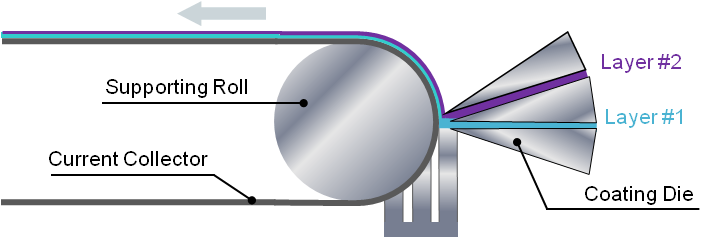
Dissolver
Capacity
20 liters
Operating speed
650 – 3,000 r.p.m.
Side scraper
inklusive
Container
single wall / doule wall
Weight
420 kg
Dimensions (LxWxH)
1,220 mm x 1,100 mm x 920 mm
In the world of slot die coating, thin is in. Or, to be precise, thin AND accurate is in. According to Scott Zwierlein of Frontier, 'roll-to-roll slot die coating has become the industry standard for extremely thin and extremely accurate coating.' Let's take a look to see if it's the right coating method for you.
'The use of slot die coating will increase because it has several advantages,' adds coating industry guru Dr. Edward Cohen. These include attributes such as excellent quality and uniformity, and the fact that it's pre-metered so that all of the coating is applied to the substrate.
However, Cohen also notes that each converter has their own specific needs which will determine which coating methods should be used. So how do you determine if slot die is the coating method of choice for you?
Let's take an in-depth look at the technology and the uses to find the answer. (Full disclosure – Scott and Frontier are a subsidiary of Delta ModTech.)
How Thin is Thin and How Accurate is Accurate?
The fields of electronics, medical devices and pharmaceuticals continue to push the envelope, or should we say, the tolerances required for converters. At some point, their needs have exceeded the capabilities of traditional extrusion dies, and entered into the realm of the nearly infinitesimal.
Slot die coating can meet these new thickness and accuracy requirements. Just how thin can slot die go? With a slot die, Zwierlein explains you can achieve an attainable wet coating thickness of <2 micron. (NOTE: Slot die can be used to coat thick as well — we're just highlighting the thin capabilities in this post.)
To put that in perspective, a 'micron,' which is the abbreviated term for 'micrometers,' is one millionth of a metre (or one thousandth of a millimetre, 0.001 mm, or about 0.000039 inch). A human hair is about 75 microns across.
Here's a picture of a carbon filament 6 microns in diameter, overlaid on a human hair 50 microns in diameter.
Photo of a carbon filament, 6 microns in diameter, overlaid on a human hair, 50 microns in diameter. – Micro photo courtesy of Wikipedia.com
And how accurate is accurate? Accuracy in the coating world is flatness. Or, in other words, how much the thickness varies from your target. The attainable transverse web accuracy with a slot die is <2%.
Talk about little margin for error.
Now listen to this short audio interview with Scott Zwierlein, and then read on how slot die delivers on thin and accurate:
https://deltamodtech.com/wp-content/uploads/2016/12/Scott-Zwierlein.mp3
1. Extremely Thin
As Zwierlein notes, 2 microns is the 'Holy Grail of liquid coatings.' Many traditional methods exist, but only slot die can achieve this level.
Why? It's the nature of the equipment design. Other methods will flood a large amount of coating, and then wipe it away. Slot die does the opposite. It applies the exact amount to the substrate. Everything the pump delivers is applied to the substrate – there is no waste.
Other methods – such as reverse roll, knife over roll, and comma coating – use a device to wipe away excess coating leaving just the thickness desired. In this scenario you're requiring a blade or bar to be positioned2 microns away from a substrate. 'That's almost impossible,' Zwierlein said. Take a look at the photo of the human hair above and you'll see what he means.

2. Extremely Accurate
Accuracy is based on the amount of material you want to put down, how close you are, and how uniform you want it to be. Zwierlein explains that you might be able to achieve 2 microns with other methods, but you can't match the accuracy of slot die.
With other coating methods the gap set for the blade or the bar is fixed and the substrate and coating fluid pass through it. If the substrate thickness varies, the thickness will vary. 'The substrate you coat on is never that flat,' he said.
The Important Attributes of Slot Die Coating
A number of attributes need to be present to help slot die deliver on its promise. These attributes result in significant benefits over traditional methods in terms of functionality and cost savings.
1. Precision pre-metered fluid delivery
2. Extremely flat and straight die surfaces
3. High-precision backing roll

4. Accurate and precise positioning of die to the substrate
5. Contamination-free environment
Industries for Slot Die Coating
Slot die is becoming increasingly necessary in a number of industries. Here are just a few specific applications:
Micro-electronics: Flat panel displays, thin circuits.
Batteries and capacitors: Lithium-ion battery electrodes, multilayer ceramic capacitors.
Barrier films: In food and medical packages, liquid film coatings are being applied to food coating.

Solar photovoltaic: Solar cells require thin coatings.
Medical diagnostics: Chemistries and other solutions need to be accurately applied. Variations in thickness can result in variations in results.
Transdermal and oral pharmaceuticals: The more accurate you coat the transdermal, the more accurate the dosage.
Now let's take a specific look at two types of slot die coating that can deliver for these applications:
Stripe Coating
Stripe coating is the preferred method when you are producing a narrow strip with exposed foil along one or both edges, in battery and capacitor applications for example.
Some requirements for good stripe coating include:
Slot Die Coating Head Design
Uniform Coating Thickness
Proper cavity design is essential. You need proper die shim thickness for optimized die pressure; that produces the right uniformity for cross web production.
Accurate Width Control and Good Edge Quality
The shim sets width — it looks like a comb. Accurate shim design and fabrication is important to maintain the proper alignment. A die vacuum is used to fine-tune the width. The die vacuum also ensures there is no saw tooth or waviness.
Patch Coating
With patch coating, we're expanding on the issues that make stripe coating desirable. It's required when an uncoated substrate is required around the full perimeter of a coated part, not just on two sides or one side.
For example, on a touch screen or an LCD screen, you may have a grid of circuitry that requires leads to be exposed on the bottom and/or the sides. Transdermal patches require patches to be cut out of adhesives, and you don't want to apply the medicine beyond the patch area.
Some requirements for good patch coating include:
Good Machine Direction Edges
The coating edges must be continuous, consistent and sharp.
Slot Die Coating Designs
Good Leading Edge
There can be no heavy build-up at the start of the patch. Accurate and repeatable timing is important – this is why it's desirable to move the fluid, and not the machine. (Scott describes this method in the audio interview.)
Good Trailing Edge
The trailing edge should be straight and clean, no feathers or drip lines.
Uniform Coating Thickness Throughout Patch
Minimal variability is essential.
Here's a graphic of a patch to illustrate some of the terms from above:
Slot Die Coating is a Huge Advantage for the Right Industries
As we noted earlier, industries such as electronics, medical devices and pharmaceutical keeping raising the bar. Converters looking to meet tighter tolerances are finding yesterday's traditional extrusion dies can't keep pace with the new normal.
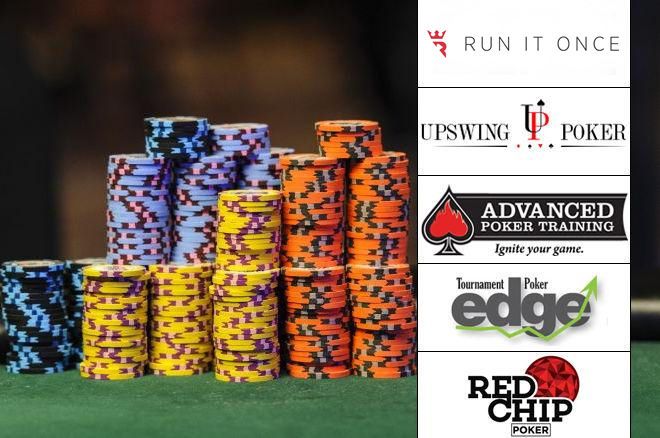
PDF download product brochure
Coatema Test Solution
PDF downloadpresentation
Coatema – The Test Solution
Easycoater
Coating systems
Doctor blade
Slot die system
Screen printing
Working width
max. 360 mm x 360 mm
Operating speed
ca. 0.4 – 4 m/min.
Dryer temperature
max. 120°C
Design
IP54 / EEx
Dimensions (LxWxH)
1,920 mm x 1,220 mm x 1,920 mm
Smartcoater
Coating systems
Knife system
Slot die system
Rotary screen system
Engraved roller system
Micro roller system
Dipping system (Foulard)
Working width
300 mm
Roller width
350 mm
Operating speed
0.1 – 10.0 m/min.
Tensile strength
10 – 250 N
Dryer
Hot air
Dryer temperature
max. 235°C
Exhaust Air / Consumption of nitrogen atmosphere
325 m3/h
Design
Atex / IP54
Dimensions (LxWxH)
5,500 mm x 1,050 mm x 1,855 mm
Basecoater
Coating systems
Slot die system
Double-sided-slot die system
Dipping system (Foulard)
2-roller system
Working width
300 mm
Roller width
350 mm
Operating speed
0.1 – 5 m/min.
Tensile strength
25 – 250 N
Dryer
Hot air
Dryer temperature
max. 235°C
Dimensions (LxWxH)
5,100 mm x 1,350 mm x 3,000 mm
Click&CoatTM
Coating systems
Slot die system
Knife system
Kisscoater
Engraved roller system
3-roller system
Screen printing
Powder scattering system
Working width
500 mm
Roller width
600 mm
Operating speed
0.1 – 2 m/min.
Tensile strength
10 – 250 N
Dryer
Hot air (UV, IR on demand)
Dryer temperature
RT – 235 °C
Exhausting air
ca. 1,500 m3/h
Design
Atex / IP54
Dimensions (LxWxH)
depends on combination
Linecoater
Coating system
Reverse Commabar
Working width
700 mm
Roller width
800 mm
Operating speed
3 – 30 m/min
Tensile strength
100 – 1.000 N
Dryer temperature
max. 180°C
Air circulation
5.000 m3/h per section
Exhaust air
5.000 m3/h per section
Dimensions (LxWxH)
19,000 mm x 2,500 mm x 2,600 mm
Red rock casino richmond bc canada. Visit the River Rock Casino Resort in Richmond BC for an unrivaled, ultimate entertainment experience. At this time, River Rock Casino Resort does not yet have approval to reopen Casinos in the Province of BC and therefore the date that we will be reopening our resort is yet to be determined.
Universal Coater
Coating systems
2 x 3 Roller system (for under and upper side)
1 x Slot die system
1 x Knife system
Working width
500 mm
Roller width
600 mm
Operating speed
1.0 – 30 m/min.
Tensile strength
75 – 3,500 N
Dryer
1) Floating dryer inert, Exhaust: 2,500 m³/h, Circulating air: 2500 m³/h
2) Conventional hot air dryer, Exhaust: 2,500 m³/h
Dryer temperature
1) Floating dryer inert: 140 °C
2) Conventional hot air dryer: 235 °C
Air circulation
2 x 6.000 m3/h
Exhaust air / Consumption of nitrogen atmosphere
270 m3/h
Design
Partially Atex / IP54
Dimensions (LxWxH)
19,000 mm x 3,500 mm x 2,700 mm
Deskcoater
Coating systems
Intermittend coating
Working width
500 mm
Roller width
600 mm
Operating speed
0.2 – 2 m/min.
Tensile strength
25 – 250 N
Dryer
Hot air
Dryer temperature
235 °C
Exhaust
ca. 2.500 m3/h
Design
IP54 / EEx
Dimensions (LxWxH)
4,250 mm x 1,600 mm x 3,100 mm
Dissolver
Capacity
20 liters
Operating speed
650 – 3,000 r.p.m.
Side scraper
inklusive
Container
single wall / doule wall
Weight
420 kg
Dimensions (LxWxH)
1,220 mm x 1,100 mm x 920 mm
In the world of slot die coating, thin is in. Or, to be precise, thin AND accurate is in. According to Scott Zwierlein of Frontier, 'roll-to-roll slot die coating has become the industry standard for extremely thin and extremely accurate coating.' Let's take a look to see if it's the right coating method for you.
'The use of slot die coating will increase because it has several advantages,' adds coating industry guru Dr. Edward Cohen. These include attributes such as excellent quality and uniformity, and the fact that it's pre-metered so that all of the coating is applied to the substrate.
However, Cohen also notes that each converter has their own specific needs which will determine which coating methods should be used. So how do you determine if slot die is the coating method of choice for you?
Let's take an in-depth look at the technology and the uses to find the answer. (Full disclosure – Scott and Frontier are a subsidiary of Delta ModTech.)
How Thin is Thin and How Accurate is Accurate?
The fields of electronics, medical devices and pharmaceuticals continue to push the envelope, or should we say, the tolerances required for converters. At some point, their needs have exceeded the capabilities of traditional extrusion dies, and entered into the realm of the nearly infinitesimal.
Slot die coating can meet these new thickness and accuracy requirements. Just how thin can slot die go? With a slot die, Zwierlein explains you can achieve an attainable wet coating thickness of <2 micron. (NOTE: Slot die can be used to coat thick as well — we're just highlighting the thin capabilities in this post.)
To put that in perspective, a 'micron,' which is the abbreviated term for 'micrometers,' is one millionth of a metre (or one thousandth of a millimetre, 0.001 mm, or about 0.000039 inch). A human hair is about 75 microns across.
Here's a picture of a carbon filament 6 microns in diameter, overlaid on a human hair 50 microns in diameter.
Photo of a carbon filament, 6 microns in diameter, overlaid on a human hair, 50 microns in diameter. – Micro photo courtesy of Wikipedia.com
And how accurate is accurate? Accuracy in the coating world is flatness. Or, in other words, how much the thickness varies from your target. The attainable transverse web accuracy with a slot die is <2%.
Talk about little margin for error.
Now listen to this short audio interview with Scott Zwierlein, and then read on how slot die delivers on thin and accurate:
https://deltamodtech.com/wp-content/uploads/2016/12/Scott-Zwierlein.mp3
1. Extremely Thin
As Zwierlein notes, 2 microns is the 'Holy Grail of liquid coatings.' Many traditional methods exist, but only slot die can achieve this level.
Why? It's the nature of the equipment design. Other methods will flood a large amount of coating, and then wipe it away. Slot die does the opposite. It applies the exact amount to the substrate. Everything the pump delivers is applied to the substrate – there is no waste.
Other methods – such as reverse roll, knife over roll, and comma coating – use a device to wipe away excess coating leaving just the thickness desired. In this scenario you're requiring a blade or bar to be positioned2 microns away from a substrate. 'That's almost impossible,' Zwierlein said. Take a look at the photo of the human hair above and you'll see what he means.
2. Extremely Accurate
Accuracy is based on the amount of material you want to put down, how close you are, and how uniform you want it to be. Zwierlein explains that you might be able to achieve 2 microns with other methods, but you can't match the accuracy of slot die.
With other coating methods the gap set for the blade or the bar is fixed and the substrate and coating fluid pass through it. If the substrate thickness varies, the thickness will vary. 'The substrate you coat on is never that flat,' he said.
The Important Attributes of Slot Die Coating
A number of attributes need to be present to help slot die deliver on its promise. These attributes result in significant benefits over traditional methods in terms of functionality and cost savings.
1. Precision pre-metered fluid delivery
2. Extremely flat and straight die surfaces
3. High-precision backing roll
4. Accurate and precise positioning of die to the substrate
5. Contamination-free environment
Industries for Slot Die Coating
Slot die is becoming increasingly necessary in a number of industries. Here are just a few specific applications:
Micro-electronics: Flat panel displays, thin circuits.
Batteries and capacitors: Lithium-ion battery electrodes, multilayer ceramic capacitors.
Barrier films: In food and medical packages, liquid film coatings are being applied to food coating.
Solar photovoltaic: Solar cells require thin coatings.
Medical diagnostics: Chemistries and other solutions need to be accurately applied. Variations in thickness can result in variations in results.
Transdermal and oral pharmaceuticals: The more accurate you coat the transdermal, the more accurate the dosage.
Now let's take a specific look at two types of slot die coating that can deliver for these applications:
Stripe Coating
Stripe coating is the preferred method when you are producing a narrow strip with exposed foil along one or both edges, in battery and capacitor applications for example.
Some requirements for good stripe coating include:
Slot Die Coating Head Design
Uniform Coating Thickness
Proper cavity design is essential. You need proper die shim thickness for optimized die pressure; that produces the right uniformity for cross web production.
Accurate Width Control and Good Edge Quality
The shim sets width — it looks like a comb. Accurate shim design and fabrication is important to maintain the proper alignment. A die vacuum is used to fine-tune the width. The die vacuum also ensures there is no saw tooth or waviness.
Patch Coating
With patch coating, we're expanding on the issues that make stripe coating desirable. It's required when an uncoated substrate is required around the full perimeter of a coated part, not just on two sides or one side.
For example, on a touch screen or an LCD screen, you may have a grid of circuitry that requires leads to be exposed on the bottom and/or the sides. Transdermal patches require patches to be cut out of adhesives, and you don't want to apply the medicine beyond the patch area.
Some requirements for good patch coating include:
Good Machine Direction Edges
The coating edges must be continuous, consistent and sharp.
Slot Die Coating Designs
Good Leading Edge
There can be no heavy build-up at the start of the patch. Accurate and repeatable timing is important – this is why it's desirable to move the fluid, and not the machine. (Scott describes this method in the audio interview.)
Good Trailing Edge
The trailing edge should be straight and clean, no feathers or drip lines.
Uniform Coating Thickness Throughout Patch
Minimal variability is essential.
Here's a graphic of a patch to illustrate some of the terms from above:
Slot Die Coating is a Huge Advantage for the Right Industries
As we noted earlier, industries such as electronics, medical devices and pharmaceutical keeping raising the bar. Converters looking to meet tighter tolerances are finding yesterday's traditional extrusion dies can't keep pace with the new normal.
If you're in these uber-competitive industries, slot die coating can be the answer you're looking for. And since 'profitable' is always in vogue, it's an advancement that will be welcomed with open arms.
Choose the right methodology for your next coating project.